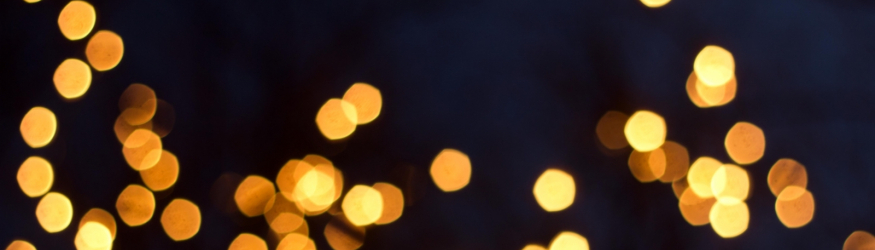
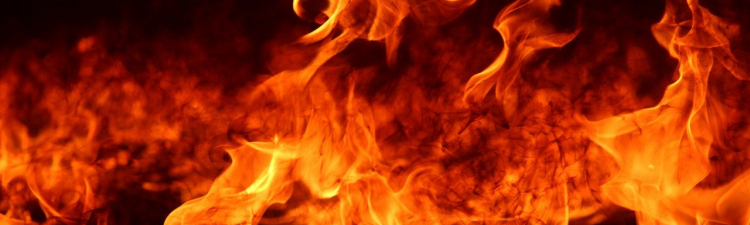
By Ben Hiller | Tue, June 15, 21
Refrigerant is the lifeblood of an HVAC system, absorbing and releasing heat to keep our homes and buildings cool in the summer and warm in the winter. This “juice” that runs through the refrigeration cycle comes in many chemical forms, each with particular safety considerations. Throughout history, scientists have chased safer refrigerants.
With the invention of modern air conditioning in the early 1900s, chemicals such as ammonia, sulfur dioxide, and methyl chloride were used despite their flammability and toxicity. The introduction of chlorofluorocarbons (CFCs) in the 1920s vastly reduced flammability and toxicity, but turned out to have ozone depletion potential (ODP) that threatened life on earth. The next round of replacement chemicals, hydrofluorocarbons (HFCs) and hydrochlorofluorocarbons (HCFCs), were later found to have global warming potential (GWP), another threat to life on earth. Although the issue of flammability was largely eliminated, the HVAC industry now finds itself considering the acceptable limits of flammability in refrigerants once again as we seek to use chemicals with low or no ODP or GWP going forward.
Why Flammable Refrigerants?
Congress passed the AIM Act (American Innovation in Manufacturing) in 2020 with the goal of phasing down HFC production by 85 percent over 15 years, putting some in the HVAC industry between a rock and a hard place. Common high pressure systems like rooftops, split systems, variable refrigerant flow (VRF), and other heat pumps do not have a readily available non-flammable alternative refrigerant. As rated by ASHRAE (American Society of Heating, Refrigerating and Air-conditioning Engineers) Standard 34, the safety classification of the most commonly used high pressure refrigerant, R-410A, is A1. As shown in the chart below, A is the lowest toxicity class, and 1 is the lowest flammability class. Common alternatives like R-32 and R-454B are class A2L, “lower flammability.”
ASHRAE Standard 34 Safety Classes
http://www.gotempstar.com/go/index.asp?id=4541
The Air-conditioning, Heating, and Refrigeration Institute (AHRI) petitioned the Environmental Protection Agency (U.S. EPA) to impose a 750 GWP limit starting January 1, 2025 for newly manufactured stationary air conditioning equipment, and January 1, 2026 for new VRF equipment. That will give ample time for manufacturers to select a replacement for R-410A, which has a GWP of 1,924. Building codes must also be updated in time to allow for A2L refrigerants.
What Does This Mean for Firefighters?
To ensure that firefighters are no more at risk with A2L than A1 refrigerants, AHRI teamed up with the UL Firefighter Safety Research Institute and members of the fire service to test the differences between refrigerants in real fire scenarios. While a typical car could have three pounds of refrigerant, a residential air conditioning system could have 20 pounds of refrigerant, and a commercial building may have hundreds of pounds of refrigerant circulating through its system. Researchers wanted to test the worst case scenario for a commercial building fire. One test aimed to quantify the amount of heat refrigerant added to a fire, called the “heat release rate,” found that it was actually higher for R-410A than for R-32. The heat added by refrigerant was about the same as a small plastic trashcan fire. There was no flash fire or deflagration observed. Another test simulated firefighters approaching a room with an air conditioning unit on fire from a hallway, and found that there was no significant difference in the heat flux in the hallway when comparing A1 and A2L. Inside the room, the baseline fire raised ceiling temperatures from ambient to about 165F before the release of refrigerant, which increased between 9F and 18F with the release of refrigerant. These tests showed that approaching and fighting a fire was not significantly different with A2L refrigerants.
After a fire is extinguished, “overhaul” operations often involve cutting walls, floors, and ceilings to investigate and stop potential spread of fire. One test sprayed refrigerant into a flame to simulate a firefighter causing a catastrophic line break, and there was no visually noticeable change in the flame size, regardless of the refrigerant used. To determine the level of refrigerant needed to cause a large flame, researchers ignited a pooled layer of refrigerant at about five times over the allowable limit. In a real fire, circumstances often exceed code allowable limits. Even then, the flame spread slowly, and there was no fireball or deflagration in the room. The experiments demonstrated that the hazard associated with A2L refrigerants is not significantly higher than that associated with the A1 refrigerants they are replacing.
What are Some Lessons Learned for the Fire Service?
Refrigerants pose a hazard regardless of their flammability class, and firefighters should assume that refrigerants are present and flammable in a fire. Leaked refrigerant evaporates quickly, and it is difficult to see any vapor at all or hear a hissing sound. Therefore, it is best to ventilate the space as quickly and efficiently as possible once the fire is put out. Spraying water on both A1 and A2L refrigerants can form hydrofluoric acid which is hazardous when inhaled or exposed to skin. Firefighters should wear full PPE with respiratory protection through all phases of response. Our firefighters can save the day while “lower flammability” A2L refrigerants save the planet from global warming.
For more information on the tests conducted by AHRI, the UL Firefighter Safety Research Institute, and members of the fire service, please see Report 8028 and online training for firefighters. For NEEP’s latest paper on refrigerants please see Informing the Evolution of HVAC Refrigerants.