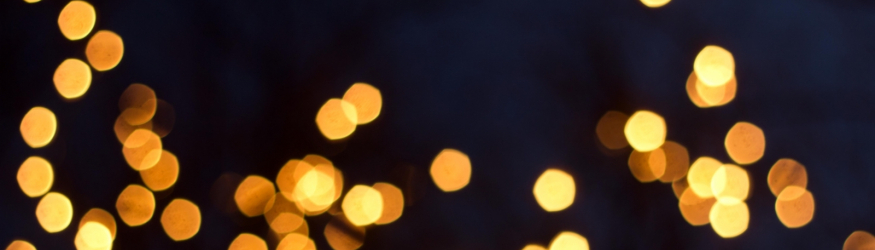
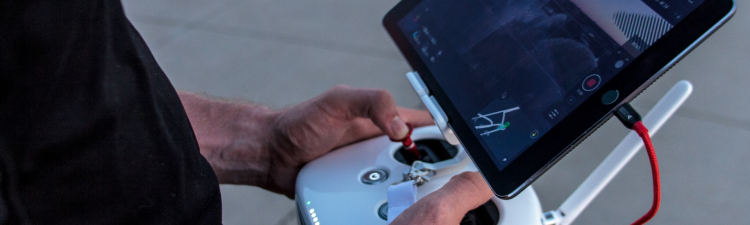
By Cornelia Wu | Mon, December 19, 22
Remote Virtual Inspections (RVI) are a hot topic. RVI are like regular inspections, in that code officials or third-party inspectors are able to review building sites in “real-time” and use that information to determine whether a component of a building meets code. RVI are different, however, because technology is used to allow inspectors to conduct reviews from off-site, whether from down the street or in another state. Jurisdictions in these states have already implemented RVI: Arizona, California, Florida, Kansas, Nevada, New York, and Texas, among others.
Advantages of RVI include time savings, cost savings, more efficient use of scarce inspector capacity, increased access to certain building spaces, and lower safety risks. These savings can be seen in less travel time, less vehicle wear and tear, and less use of fuel. Eliminating the need for inspector travel also increases the capacity of code officials. RVI allow jurisdictions to maximize efficiency of existing code officials as the industry faces a shortage in the workforce.
Conversely, there are a few disadvantages with RVI. One is the need for an extra interface between inspectors and sites – for example, inspectors may need to verbally direct contractors or homeowners to move or zoom camera views, and to take still photos for submission when requested. Another potential disadvantage is the need for a high-speed cellular or wi-fi connection, which may present a barrier to the use of RVI in some areas.
Inspections That May be Conducted by RVI
A sampling of inspections being conducted via RVI in various jurisdictions includes, but is not limited to:
-
Limited components of construction such as concrete slab, foundation wall, partial framing, insulation, vapor retarder, ducts and duct sealing;
-
Window/door replacements;
-
Installation/replacement of plumbing or heating and air-conditioning equipment, such as hot water heaters;
-
Mechanical ventilation;
-
Repairs or upgrades of electrical services;
-
Sewer line repairs;
-
Lighting;
-
Rooftop solar;
-
Pool and spa; and
-
Additions, alterations, repairs and changes of occupancy to existing buildings.
RVI do not replace all of the inspections for a given building site. Some building components continue to require on-site inspection; the number and type will depend on the jurisdiction. For instance, some jurisdictions require footing inspections to be conducted in person.
Requirements of RVI
Jurisdictions (and code officials or third-party inspectors) should have:
-
Access to Electronic Plan Filing within the jurisdiction prior to use of RVI;
-
Relevant documents (approved plans and revisions, forms, certificates) for the scope of work being inspected;
-
Decisions on which inspections qualify for RVI, and decisions on whether or not the audio/visual information transmitted through the inspection process are retained;
-
A quality control policy, including a policy on whether inspectors may override a RVI and require an in-person site visit;
-
A viewing screen such as computer monitor or tablet with sufficient resolution to review the components being sent from job sites per requirements below, and an audio connection;
-
A stable internet connection with good LTE or 4G or 5G cellular or full strength wi-fi connection;
-
If required by access restrictions, drones may be considered. When using drones, one must be aware of and comply with all Federal Aviation Administration (FAA) regulations. Drones under 55 pounds may have less restrictive regulations than those over 55 pounds (typically a drone used in RVI might be 10-15 pounds).
Individuals at the job site communicating with inspectors should have:
-
Relevant permit documents;
-
Good lighting, whether permanent or temporary, flashlight, ladder, electric tester, tape measures, and other tools normally needed during a building inspection;
-
An audio/video recorder (video camera, tablet, smart phone) with minimum 1080p, 60 frames per second, enough memory to complete the inspection, and either fully charged battery or additional power supply; and
-
Stable internet connection with good LTE or 4G or 5G cellular or full strength wi-fi connection.
Advantages for Off-site Construction
RVI can also be deployed to support the use of off-site construction. Off-site construction includes pre-cut lumber, panelized walls, and modular components. It does not include manufactured (HUD) housing, which is subject to separate federal regulations. Off-site construction drives efficiencies because it is fabricated in a facility under controlled conditions, and components for many buildings and homes are built together in a single factory. Often the factory is in a different jurisdiction (or state) than the authority having jurisdiction (AHJ), which is local to the job site. Under these conditions, AHJs often hire third-party inspectors to visit the factory. Alternatively, they can use RVI.
Conclusion
A frequently cited reason for use of RVI is efficiency – both in time and cost. RVI allow code officials to schedule inspections with less buffer time between them due to lack of travel, allowing for more inspections in a day. Increased availability of inspections saves time and money on job sites, because installing drywall, for instance, cannot happen until after inspection of the wall components (plumbing, electrical, insulation, etc.). RVI also show promise for additional applications: for instance, in some states, areas with low population also see slow code adoption and low code enforcement, due to long travel times for inspectors. RVI will ultimately increase the reach of code officials and inspections, in terms of applicability, frequency, and geography.
A lack of consistent universal standards has presented barriers to further implementation of RVI. NEEP is developing resources to explain RVI to jurisdictions, code officials, and builders, and coordinating with the International Code Council on RVI protocols. For further information on RVI, NEEP published RVI: Challenges and Opportunities in October 2021. More materials will be forthcoming.