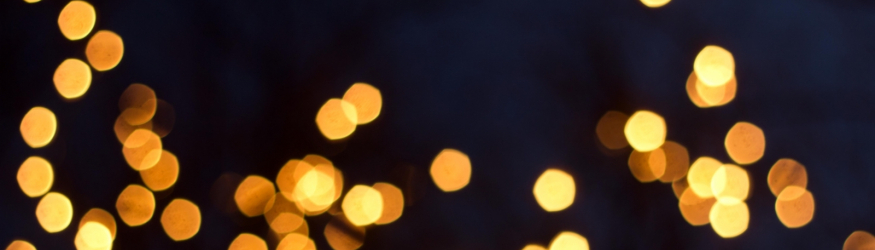
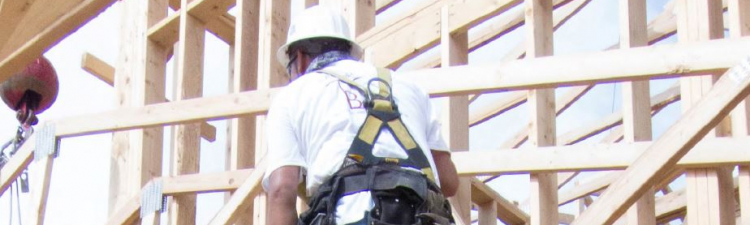
By Cornelia Wu | Wed, March 23, 22
By now we’ve all heard that buildings are a big energy user and emit a large proportion of greenhouse gases in both the U.S. and the world. But do buildings need to be a climate change problem? How can off-site construction be part of the solution?
What is on-site construction? It is the most common method of construction, where all of the construction materials - such as cast-in-place concrete, lumber, plywood, insulation, windows, doors, drywall, electrical, and plumbing - are brought to the site and assembled sequentially in their permanent location.
What is off-site construction? The name may be a little deceiving, since even off-site construction needs to be built partially on-site. But the off-site portion of the construction can create lots of opportunities for positive change. In off-site construction, part of the building is put together in a factory, while the rest of the building is put together on-site. There are three major categories of off-site construction: precut, panelized, and modular. Each of these categories fabricates more and more parts of the building at the factory. These parts are then transported to a prepared site for final assembly and installation at the building’s final location.
Statistics from the U.S. Census Bureau show that only three percent of single-family homes in the U.S. are built using off-site construction. This may be in part because, despite many benefits, there are many misconceptions about off-site construction. The most common misconceptions are that off-site construction is low-quality and that it creates cookie-cutter designs. In the past, in order to achieve economies of scale, modules were often overly repetitive. Today’s off-site construction is centered on quality, design flexibility, and often delivers projects that are indistinguishable from site-built houses. The evolution of the use of digital design tools by architects and engineers has allowed for greater customization. Surveys by industry groups and NEEP’s Technical Advisory Group show that the biggest barriers to adoption of off-site construction are inertia in the building sector, a lack of contractor familiarity and experience, and regulatory issues posed by codes and different permitting, inspection, and zoning processes.
Off-site buildings can be created in more sustainable ways, and they function in an energy efficient manner throughout their life cycle. Building materials such as lumber are cut in a factory environment instead of on-site. As a result, precision cutting and the ability to re-use scrap in other parts of the factory significantly reduce waste and cost. This allows material re-use and reduces the number of dumpsters transporting construction waste from the construction site straight to the landfill. Precision cutting also allows for tighter fits between building components, allowing for a tighter building envelope (which seals off the exterior of the building from the interior), reducing energy use over the life of the building. The factory itself is protected from the weather in a way a building site is not, shielding the building components from moisture infiltration, future mold problems, and material degradation. The building site can be prepared simultaneously with the fabrication of multiple building parts in the factory, speeding up the timeframe. This contributes to less overall site disruption, with benefits ranging from less pollution from construction vehicles to less contamination in stormwater runoff from the site. For this reason, modular and panelized construction is particularly well-suited to greenfield sites or urban infill sites. The conceptual diagram below shows how an off-site schedule saves time over a traditional on-site schedule.
There are also workforce opportunities in off-site construction. There has been a labor shortage in the construction industry for many years. On top of that, the construction workforce is aging. The lack of skilled labor has had an effect on the affordability of homes. One solution is modular construction, because it increases construction efficiency. A new workforce must be trained to fill the labor shortage. Factory assembly of panelized and modular houses lends itself to training a greater pool of people to take these roles. Manufacturers need to reach out to a more diverse workforce, including older workers, women, and Black, Indigenous, and people of color (BIPOC).
Off-site construction’s many advantages include energy efficiency, time and material savings, less disruption of project sites, reduced emissions from construction, and job opportunities. Energy efficiency in particular has long-term effects on the total use of energy by a building over its life cycle. Better education should be available to builders, architects, building department and code officials, as well as homeowners about off-site construction. As we continue to explore and embrace both new and old ways of designing and building structures, we need to keep our eyes on the goals of reducing emissions and preventing climate change.